Le moteur thermique est condamné... et c'est une excellente nouvelle !
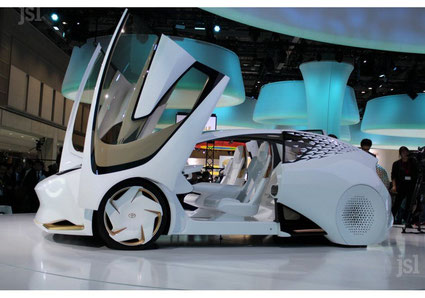
Le Salon de Tokyo 2019 (jusqu'au 4 novembre) vient confirmer l'avènement proche de cette révolution technologique et économique.
Les Japonais, très peu présents aujourd'hui dans le "tout électrique", arrivent en force : Toyota, Nissan, Mazda, Lexus... y présentent une kyrielle de véhicules et de concept car électriques, à 4, 3 ou deux roues.
C'est bien le signe que le fruit est mûr !
Comme l'écrit le journal Le Monde : " Il faut croire que, partout dans le monde, l’électrification accélérée de l’automobile constitue un horizon indépassable."
Pourquoi ?
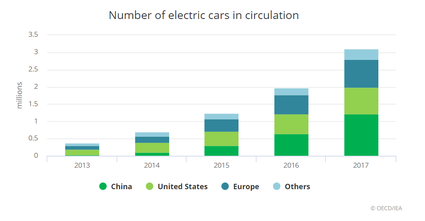
Les raisons sont à la fois politiques et économiques.
Le moteur thermique, avec les émissions qui l'accompagnent, a mauvaise presse ; partout dans le monde des associations, des citoyens, se mobilisent. Les politiciens ne peuvent ignorer ce qui tend à devenir un mouvement de masse.
D'ici 2025, la Norvège souhaite que 100% de ses voitures soient des unités hybrides électriques ou hybrides. Les Pays-Bas prévoient d'interdire toutes les ventes de voitures à essence et à moteur diesel d'ici la même année. En 2030, l'Allemagne envisage d'interdire les moteurs à combustion interne. La France et la Grande-Bretagne visent à mettre fin à leurs ventes de voitures à essence et à moteur diesel en 2040. La Chine, actuel leader dans le domaine de la voiture électrique, avance à marche forcée.
La décarbonisation est plus que jamais à l'ordre du jour pour faire face à l'urgence du changement climatique.
Cependant, pour que le véhicule électrique soit propre, deux conditions doivent au minimum être remplies :
- que les réseaux électriques soient principalement alimentés par des énergies renouvelables.
Actuellement, la part de l’énergie renouvelable dans le monde est passée de 22% en 2001 à 33%. L’Europe est à 36%, la Chine à 26% et les États-Unis à 18%.
Mais la progression s'accélère, notamment grâce au solaire (voir l'article ci-dessous).
- que les matériaux constituant les batteries soient recyclés. Les projections actuelles indiquent qu'à court terme, le recyclage pourrait fournir jusqu'à 50% des matériaux nécessaires (actuellement moins de 10%) dans la chaîne d'approvisionnement des batteries lithium-ion, en réduisant les coûts jusqu'à 20%.
A partir de là, l'aspect économique intervient : très rapidement les véhicules électriques devront être moins chers et plus performants que les voitures à essence.
D'ores et déjà, pour les voitures à kilométrage élevé, telles que les taxis, qui parcourent en moyenne 70 000 km / an, le coût total de possession d'un véhicule électrique (le prix d'achat, l'assurance, le carburant et l'entretien), est bien inférieur à celui d'une voiture à essence. Cela signifie que les flottes institutionnelles et commerciales vont probablement passer très vite à l'électricité, une étape majeure dans le déploiement de l'électrification.
Pour atteindre la parité des coûts avec les voitures à essence personnelles, qui parcourent en moyenne 12 000 à 15 000 km / an, le prix des batteries doit se situer à environ 100 USD / kWh contre une valeur actuelle de 180 USD à 200 USD / kWh. Les projections pour l’année de la parité des coûts - véhicules électriques / voitures à essence - la situent avant 2025.
Comment ?
CLIQUEZ sur l'image
Le moteur de la VW ID.3 ! (200 CV)
La batterie, l'élément clé
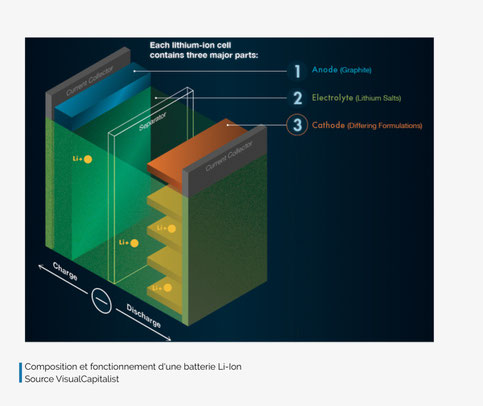
Le moteur d'une voiture électrique se distingue par sa simplicité et un coût d'entretien bien inférieur à celui d'un moteur thermique.
C'est donc la batterie qui est au coeur des investissements en recherche/développement.
Le principe de la batterie nous est connu depuis le lycée : une cathode, une anode, un électrolyte, un séparateur (membrane poreuse).
La réaction chimique, une oxydo-réduction, permet un transfert d'électrons.
La borne négative (-) correspond à l'anode, où se produit la réaction d'oxydation qui va fournir les électrons. La borne positive (+) correspond à la cathode où se produit la réaction de réduction qui va consommer les électrons.
Dans un accumulateur, ces rôles s'inversent selon que l'appareil débite (actif) ou se charge (passif).
Les cathodes et anodes d'un accumulateur sont donc alternativement positives et négatives selon leur état, charge ou décharge.
Dans le cas des batteries Li-ion qui alimentent aujourd'hui les moteurs électriques de voiture, ce sont les ions lithium (sels de lithium), qui circulent - au sein d'un solvant - entre les électrodes pour générer l’énergie.
La cathode, est principalement constituée d'un mélange de nickel, de manganèse et de cobalt, aux proportions variables. L'anode est en graphite.
Ce modèle a encore de beaux jours devant lui, mais sa technologie est actuellement en développement de façon à améliorer sensiblement la densité énergétique produite (environ 250 Wh/kg).
Partout dans le monde des équipes de recherche sont mobilisées pour obtenir des batteries Li-ion dont la densité électrique serait au moins doublée, avec une charge plus rapide, une autonomie plus longue, une durée de vie prolongée, une sécurité accrue... pour un prix inférieur !
En France le hub de l'énergie, inauguré en 2018, est le siège du Réseau sur le stockage électrochimique de l’énergie (RS2E) porté par le CNRS, qui fédère 17 laboratoires de recherche CNRS/Universités, 16 partenaires industriels et trois établissements publics (CEA, IFPEN et Ineris) spécialisés dans le transfert de technologie.
Les nouvelles batteries à électrolyte solide
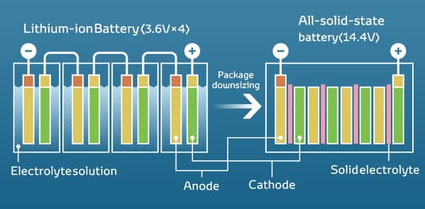
Au centre d’une multitude de programmes de recherche, la technologie de batteries tout solide est l’une des pistes les plus prometteuses et les plus avancées.
Le système repose sur une conception entièrement solide ce qui permet de se passer de solvant, évitant ainsi les risques d’incendie en cas de surchauffe ou de court-circuit, comme on a pu l'observer sur certains véhicules (Telsa) et smartphones (Samsung). De plus les batteries Li-ion supporte mal les basses températures ; à partir de -5°C des dendrites (excroissances) se forment sur l'anode, ce qui peut provoquer des courts-circuits. Enfin au-dessus de 35°C la durée de vie est affectée.
Ces nouvelles batteries promettent une autonomie comparable (800 kms) à celle des modèles à combustion interne, ainsi que des temps de charge similaires au remplissage du réservoir.
John B. Goodenough, qui vient de recevoir le prix Nobel de chimie 2019, à l'âge de 97 ans (avec Stanley Whittingham et Akira Yoshino) pour sa contribution à la mise au point de la batterie lithium-ion, vient de proposer un modèle particulièrement performant.
Dans ce modèle, l'électrolyte se compose d'une plaque de verre qui fait office de séparation entre l'anode et la cathode. L'anode peut être constituée de différents métaux (lithium, potassium ou sodium). La capacité de charge et de décharge, donc l'autonomie, est doublée, la durée de vie est augmentée. Autre point très intéressant, le temps de recharge se compte désormais en minutes et non plus en heures.
Même la plage thermique d'utilisation de la batterie solide est plus confortable : là où l'électrolyte liquide fonctionne de façon optimale pendant 15 ans à condition de ne pas dépasser 35 °C (d'où certains systèmes de refroidissement couplés aux batteries), cette batterie peut fonctionner entre -20 °C et 100 °C sans nécessiter de refroidissement.
Ce modèle, qui couple des anodes au lithium métal avec des électrolytes à l'état solide, est sur le point d'aboutir chez de nombreux fabricants.
Chaque atome d’une anode au lithium métal peut stocker et libérer de l’énergie pendant le cycle de charge-décharge, alors qu'avec les anodes en graphite actuellement utilisées dans les batteries lithium-ion, seul un atome de lithium pour six carbones peut stocker ou libérer de l’énergie.
A noter que que de nombreuses équipes travaillent sur des anodes au sodium (omniprésent sur la planète, contrairement au lithium) et qu'il n'est pas exclu que des batteries au sodium performantes soient mises sur le marché d'ici une dizaine d'années.
Ainsi Toyota a annoncé qu'il disposerait de batteries avec des anodes en lithium et des électrolytes solides pour ses véhicules électriques d'ici le début des années 2020. Les prochaines Toyota tout électrique (6 modèles sont annoncés !) en seront dotées.
En Europe, au Japon et en Chine, tous les constructeurs sont sur le pont. En Chine, des startups fleurissent et les premières chaînes de production ont démarré.
Qing Tao Energy Development Co, une startup de l’Université technique de Tsinghua, vient de créer une nouvelle ligne de production de batteries à électrolyte solide à Kunshan, dans l’est de la Chine. Les rapports indiquent que la société a atteint une densité énergétique de plus de 400Wh/kg (à comparer aux batteries lithium-ion de nouvelle génération qui sont limitées à 250-300Wh/kg).
Sa capacité de production sera de 700 MWh en 2020.
Vers une gestion plus écologique de la production des batteries Li-ion
Grâce au recyclage et à l'économie économie des métaux Li, Co et Ni
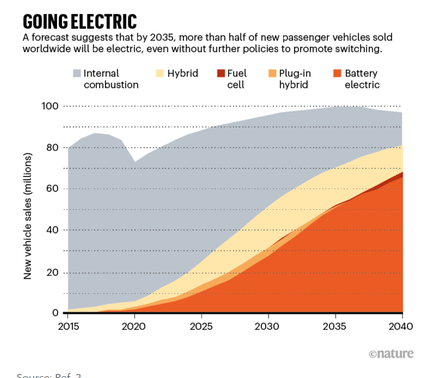
L'électrification de la mobilité personnelle s'accélère, au point que les experts prévoient que la moitié des ventes mondiales de véhicules de tourisme en 2035 seront électriques.
Ce sont sont donc des centaines de millions de véhicules électriques qui seront produits dans la prochaine décennie, avec des batteries contenant plusieurs dizaines de kg de matériaux.
Dans ce délai, ce sont toujours les batteries Li-ion qui domineront le marché, même si l'avenir plus lointain annonce des technologies plus performantes et moins coûteuses (voir sur le site).
Les chercheurs dans le domaine des matériaux travaillent donc sur deux objectifs :
- réduire la quantité de métaux dans les batteries (Li, Co, Ni). Ceux-ci sont rares, coûteux ou entraînent, au niveau de leur extraction, des coûts environnementaux et sociaux élevés.
- améliorer le recyclage des batteries, afin que ces métaux précieux puissent être réutilisés efficacement.
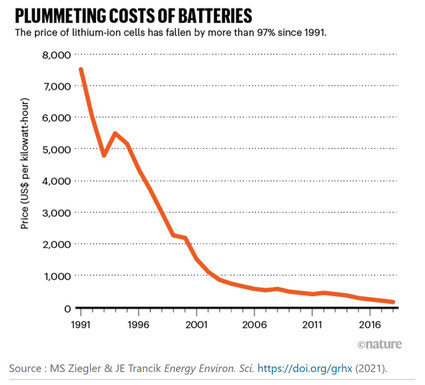
Le coût des batteries Li-ion s'est littéralement effondré en trente ans et va baisser encore. Ce n'est pas forcément une bonne nouvelle pour les recherches sur les solutions alternatives et le recyclage !
Une batterie standard récente, type NMC-532, contient 8 kg de lithium, 35 kg de nickel, 20 kg de manganèse et 14 kg de cobalt.
Le lithium, élément clé de la production d'énergie, n'est pas rare. Un rapport de juin dernier (2021) a estimé que les réserves actuelles du métal – 21 millions de tonnes, selon le US Geological Survey – sont suffisantes pour mener la conversion aux véhicules électriques jusqu'au milieu du siècle.
Ces réserves sont très certainement sous-estimées.
L'augmentation de l'exploitation minière du lithium porte ses propres préoccupations environnementales : les formes d'extraction actuelles nécessitent de grandes quantités d'énergie (pour le lithium extrait de la roche) ou d'eau (pour l'extraction des saumures).
Mais les techniques plus modernes qui extraient le lithium en utilisant l'énergie géothermique pour piloter le processus, sont considérées comme plus douces et surtout beaucoup moins dommageables pour l'environnement que l'extraction des combustibles fossiles (puits de pétrole, fracturation hydraulique...).
Comment remplacer le cobalt ?
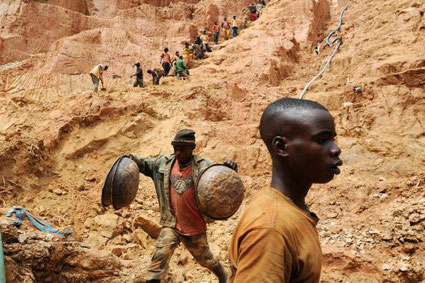
Le cobalt, est le composant le plus coûteux des batteries des véhicules électriques actuels.
Les deux tiers de l'approvisionnement mondial sont extraits en République démocratique du Congo et les militants des droits de l'homme font part de leurs préoccupations concernant les conditions de travail (le cobalt, comme d'autres métaux lourds, est toxique), et en particulier le travail des enfants.
Malheureusement, abandonner complètement le cobalt abaisse la densité énergétique d'une batterie.
Actuellement, un certain nombre de laboratoires expérimentent cependant des cathodes à faible teneur en cobalt ou sans cobalt et les experts pensent que le problème du cobalt est en passe d'être résolu à l'échelle du laboratoire.
Ainsi, Arumugam Manthiram de l'Université du Texas à Austin, a mis au point une spinelle haute tension, LiNi 0,5 Mn 1,5 O4 (LNMO) qui conserve la structure cristalline d'oxyde de cobalt des cathodes actuelles et conserve leurs performances. Il a créé une start up - TexPower - qui développe le concept.
A noter que le pionnier des véhicules électriques Tesla, basé à Palo Alto, en Californie, a annoncé son intention d'éliminer ce métal de ses batteries au cours des prochaines années.
Comment mieux recycler ?
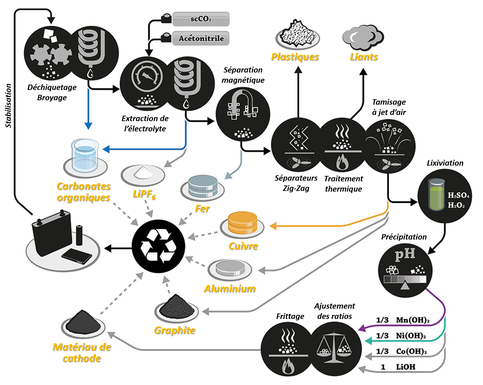
Il faut noter que lorsqu’une batterie de voiture électrique passe en dessous de 75% de ses capacités, elle est alors remplacée. En effet, cela ne suffit plus pour proposer une autonomie pertinente. Néanmoins, même à moins de 75%, les batteries sont encore fonctionnelles et peuvent servir à autre chose, notamment pour le stockage stationnaire.
Paradoxe : le recyclage des batteries actuelles n'est rentable que... grâce au cobalt !
Le lithium est récupérable mais à un coût supérieur à l'extraction.
Il faut donc des incitations financières fortes pour améliorer le recyclage.
Si les Etats-Unis et l'Europe ont renforcé la réglementation et promettent des aides, la Chine en est au stade de la concrétisation : Guangdong Brunp, basé à Foshan – une filiale de CATL, le plus grand fabricant chinois de cellules lithium-ion – peut recycler 120 000 tonnes de batteries par an.
C'est l'équivalent de ce qui serait utilisé dans plus de 200 000 voitures !
En France, la réglementation impose un recyclage à 50% d'une batterie Li-ion (90% pour une batterie au plomb), mais les industriels indiquent pouvoir recycler plus de 70% de la masse d'une batterie).
A noter que Le Groupe Renault a rejoint le consortium créé en septembre 2020 par le spécialiste de la gestion optimisée des ressources Veolia et le spécialiste de la chimie et des matériaux avancés Solvay. Les partenaires veulent mettre en place un « écosystème circulaire des métaux issus des batteries électriques en Europe »;
Dans cette optique le constructeur français va créer une "Re-Factory" à Flins qui prévoit l’installation d’une ligne de démantèlement de véhicules et batteries électriques à partir de 2024 " afin d’augmenter sa capacité à recycler et s’approvisionner en pièces et matières en boucles courtes ".
Les techniques actuelles de recyclage comportent plusieurs étapes :
- la décharge totale des modules puis le démontage,
- le broyage qui donne la masse noire (black mass) qui contient le carbone hydrophobe et les oxydes de métaux hydrophiles.
La séparation de tous les constituants s'effectue par hydrométallurgie (schéma ci-dessus) ou pyrométallurgie.
Hydrométallurgie – Les métaux sont dissous par lixiviation, principalement acide à température élevée (80°C), puis isolés par extraction liquide/liquide (par des acides organiques : Cyanex 272, D2EHPA), par précipitation, ou encore par électrodéposition. La dissolution sélective des métaux par des micro-organismes est une voie de recherche actuellement poursuivie. Les sels de métaux récupérés à la cathode peuvent être réutilisés pour la synthèse de nouveaux matériaux actifs (recyclage en boucle fermée).
Pyrométallurgie – Les modules entiers de batterie peuvent être introduits directement dans un four comportant plusieurs zones successives : i) zones de préchauffage (< 300°C) afin d’évaporer les solvants, ii) zone de pyrolyse (700°C) afin d’incinérer les plastiques (réaction exothermique) et les électrolytes (40-50% du poids de la batterie), et iii) zone de fonte permettant la réduction des oxydes de métaux en un alliage de Co, Cu, Fe et Ni et la formation de scories (Li, Al, Mn) ainsi que de gaz. Cette étape est très énergivore, exigeant des températures pouvant atteindre 1475 °C pendant 30 minutes.
La technique de séparation par hydrométallurgie peut être optimisée. La société canadienne Lithion assure pouvoir recycler 95% d'une batterie Li-ion.
Cependant des procédés radicalement différents commencent à émerger.
En particulier, les chercheurs développent un nouveau processus de recyclage connu sous le nom de recyclage direct. Le recyclage direct est la récupération, la régénération et la réutilisation des composants de la batterie directement sans détruire la structure chimique.
En maintenant la valeur de processus dans les composants de la batterie d'origine, un matériau reconstitué à moindre coût peut être fourni aux fabricants de batteries.
Cela pourrait réduire sérieusement le coût des batteries de véhicules électriques.
En fait le recyclage n'est plus vraiment un problème technique, mais un problème financier. Quand des millions de véhicules électriques rouleront, ce problème là sera résolu et le coût global d'un véhicule électrique sera bien en dessous de celui de son équivalent thermique et il sera d'un bout à l'autre de la chaîne beaucoup moins polluant.
Les batteries structurelles : le grand bond en avant
L'énergie est dans la carrosserie !
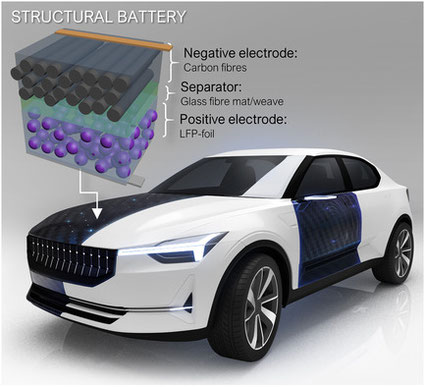
J'ai évoqué ICI quelques unes des nombreuses pistes suivies pour améliorer les batteries et notamment celles qui proposent de remplacer le lithium par le sodium ou encore les batteries à électrolyte solide.
Encore plus révolutionnaire est le concept de batterie structurelle qui permet le stockage d'énergie... sans masse et ouvre la voie aux avions électriques !
Ici, les cellules de batterie lithium-ion sont efficacement intégrées dans une structure composite, souvent de type sandwich.
Dans la voiture, c'est la carrosserie qui stocke l'énergie, d'où une économie de poids considérable !
Dans ce domaine, les chercheurs de l'Université de Chalmers (Suède) en collaboration avec le KTH Royal Institute of Technology de Stockholm, viennent de présenter une batterie structurelle avec des propriétés qui dépassent de loin tout ce qui avait été proposé jusqu'ici, en termes de stockage d'énergie électrique, de rigidité et de résistance. Ses performances multifonctionnelles sont dix fois plus élevées que les prototypes de batterie structurelle précédents.
Cette batterie contient une fibre de carbone qui sert à la fois d'électrode, de conducteur et de matériau porteur.
La batterie a une densité d'énergie de 24 Wh / kg, soit une capacité d'environ 20% par rapport aux batteries lithium-ion comparables actuellement disponibles. Mais comme le poids des véhicules peut être considérablement réduit, moins d'énergie sera nécessaire pour conduire une voiture électrique, et une densité d'énergie plus faible se traduit également par une sécurité accrue.
Enfin avec une rigidité de 25 GPa, la batterie structurelle peut vraiment rivaliser avec de nombreux autres matériaux de construction couramment utilisés.
Le constructeur américain Tesla, a fait un premier pas significatif dans cette direction en présentant en janvier dernier, sa nouvelle cellule de batterie 4680, mais également une nouvelle architecture de batterie construite autour de la nouvelle cellule.
Cette nouvelle conception réduit le nombre de pièces, la masse totale du pack batterie, et permet donc à Tesla d'améliorer l'efficacité et in fine l'autonomie de ses véhicules électriques.
La batterie structurelle devrait être utilisée pour la première fois dans le modèle Y qui sera construit à la Gigafactory de Berlin et dans le nouveau modèle S Plaid.

L'impact sur la géoéconomie
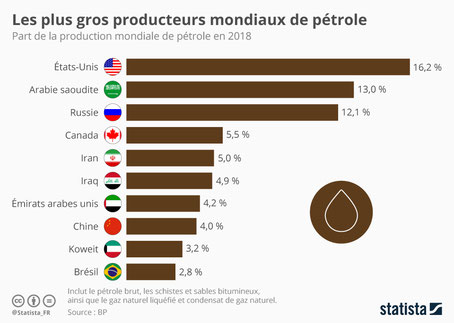
L'électrification des transports marque un tournant dans l'économie énergétique. Depuis plus d'un siècle, le pétrole est la pierre angulaire du transport et son industrie n'a cessé de croître, parallèlement à l'industrialisation et à l'amélioration du niveau de vie. Mais le pétrole est abondant dans relativement peu de pays et ceux-ci assument une importance géoéconomique démesurée car le pétrole destiné aux transports est un besoin sociétal essentiel.
L'électrification des transports signifie que le pétrole va perdre l'un de ses marchés principaux et donc son pouvoir économique et politique international.
Sur le plan économique la fin du tout pétrole est donc aussi une bonne nouvelle.
Au contraire la lumière du soleil et le vent sont disponibles partout et la production d’électricité est essentiellement une entreprise nationale.
Il reste le problème du stockage (voir ci-après) et encore une fois de la mise au point de batteries qui ne rendent pas les populations dépendantes de quelques pays gros producteurs.
Pour les véhicules électriques, actuellement, le recours au lithium (qui n'est recyclé qu'à 1% pour des problèmes de pureté) est incontournable. La figure ci-dessus montre que le minerai n'est exploité que dans très peu de pays :
- le triangle sud-américain, Argentine-Chili-Bolivie, largement dominant,
- l'Australie,
- la Chine et les Etats-Unis.
Voila pourquoi les chercheurs travaillent à marche forcée pour mettre au point une batterie sodium-ion à électrolyte solide.
Annoncée pour 2019, la Fisker EMotion (le concurrent de Tesla) ne devrait pas voir le jour avant 2021. En effet le constructeur a décidé de basculer vers la technologie de la batterie solide, grâce à une "électrode tri-dimensionnelle" capable d'offrir une capacité multipliée par 2,5 par rapport à une batterie classique lithium-ion.
L'autonomie, atteindrait les 800 km, tandis que la recharge ne demanderait qu'une minute !
Cette batterie est développée par Sakti3 , filiale à 100% de Dyson Ltd.